複合火力発電所におけるダクトバーナーの置き換え
複合火力発電所におけるダクトバーナーの置き換え
多くの複合火力発電所(CCPP)とコージェネレーションまたは熱電併給(CHP)発電所は、排熱回収ボイラー(HRSG)内の補助燃焼システム、またはダクトバーナーを利用している。ダクト・バーナーは、CCPPにおいて、メガワットを追加するために蒸気タービン発電機へのHRSG蒸気出力を迅速かつ効率的に増加させるためにオンデマンドで作動させることができ、メガワット出力は、電力需要をサポートするために生産者の該当するディスパッチからオンデマンドまたは事前に計画することができる。ダクト・バーナーはまた、顧客が使用する蒸気出力を増加させ、最終的にCHP生産者の売上を増加させることができる。
国内市場全体では、多くのダクトバーナーが1995年から2005年の間に建設されたオリジナルのグリーンフィールドCCPPとコージェネ/CHPに設置された。ダクトバーナーの設置は、2005年から2015年にかけて、グリーンフィールドのCCPPとコージェネ/CHPで減速した。2015年以降、新しいCCPPとコージェン/CHP施設の建設は、景気と、グリーン燃料技術の研究と投資を求める政府機関からの最近の圧力のために、ほぼ停滞している。その結果、国内市場全体の発電所インフラは老朽化し、注意を必要としている。
残念なことに、既存の設備インフラの老朽化により、現在設置されている多くのダクトバーナーシステムは、設計された耐用年数に達しているか、または急速に近づいており、生産者にとって次のようなさまざまな問題がある:
- 機器を修理し続けるためのメンテナンス費用の増加
- HRSGへの排ガスや火炎の衝突による運転コストの増加
- バーナーの部分的な故障により、消灯や信頼性に問題が生じる。
- バーナーの完全な故障により、バーナーが機能しなくなるという単純な問題から、バーナーがHRSGの床に倒れ込むという複雑な問題まで発生する。
- 老朽化した設備は、時間の経過とともに指数関数的な速度で劣化し続ける。
施設のダクトバーナーの現状を理解し、修理または交換のための資本コスト予算をいつ立てるべきかを知るためには、老朽化した機器の頻繁な文書化された検査と監視モニタリングが不可欠である。検査は、設備が稼動している間に実施することができるが、通常、春と秋の停電時に実施するのが最善であり、信頼できる燃焼会社によって実施されるべきである。これらの検査は、既存の機器に影響を与える可能性のある問題を特定し、既に故障が発生し ている理由を診断し、メンテナンスを継続するよりも交換する方が経済的かどうかを判断 することができる。施設の再稼働を遅らせないように適切に調整すれば、検査は最短1日で完了する。
ダクトバーナーシステムの交換は、多くの生産者が思っているよりも簡単であることが多い。これは、発電能力のライフサイクルを維持するための最良の方法となり得る。なぜなら、交換によって老朽化プロセスが止まり、生産者の時計がリセットされるため、経営陣にとって多くの心配事の一つが解消されるからである。 Zeeco 、このようなターンキー方式によるダクトバーナーシステム(図1)の交換のケーススタディは、施設所有者が診断からスタートアップまでの経路を理解するのに役立ち、発電所のインフラから老朽化した機器を排除することの利点を実証する。
状況
2022年、米国南東部の大手電力会社から、既存のダクトバーナーシステムに関する懸念がZeeco 。Zeeco 、停電検査を実施し、以下のような調査結果を記録した:
- 歪んだフレームスタビライザー
- バーナーエレメントの主燃料炎のパイロット点灯不良
- 火炎スキャナーの認識不良
- 下流のHRSGチューブ部分への火炎衝突
反りや歪みのある火炎安定器は、タービン排気ガス(TEG)の流れが悪いために火炎形状を制御できないことから生じることがある。これは一般に、新しい技術が導入されるまで、常に不十分でありながら知られていなかった古い設計によって引き起こされる。何年もオンとオフを繰り返す燃焼装置の単純な経年変化も、フレームホルダーやブラフボディを摩耗させる。今回のケースでは、この両方が機器の腐敗の原因として指摘された。
パイロットが主燃料炎に点火できないのは、バーナーエレメントのたるみが原因です。この故障のその他の原因としては、極端な温度で連日HRSG炉内に存在するスパーク装置の破壊が挙げられる。高エネルギー点火システムの一般的な電気回路は、TEGや開放導管システムからの水蒸気によって簡単に破壊される。このケースでは、バーナーエレメントのたるみが、パイロットが主燃料に点火できなかった主な原因だった。火花の先端が主燃料の通り道に入らなくなり、点火するチャンスがなくなったのだ。
主燃料炎の火炎スキャナーの認識不良も、いくつかの問題に起因している可能性がある:
- バーナーエレメントのたるみ。
- フレームスキャナーのレンズに汚れ、ゴミ、水蒸気が付着している。
- HRSGの通常の激しい振動によるフレームスキャナーの取り付けシステムの意図しない動き。
電子部品は長持ちせず、炎を正しく認識できない原因になりやすい。
この場合、スキャナーは古い技術で、複数のバーナー高所にわたってさまざまな段階で摩耗していた。
下流のHRSG管セクションへの火炎衝突は、HRSGボイラーの主要な破壊要因であり、長い合金ボイラー管の修理に数百万ドルの費用がかかります。バーナーシステムが原燃料をHRSG炉に導入し(バーナー管理システム[BMS]の完全制御下)、パイロットイグナイターによって点火されると、長くのんびりとした炎が火炎衝突を起こします。主燃料炎が点火され、火炎スキャナーによって認識されると、HRSG分散制御システム(DCS)により、出力蒸気需要に合わせて燃料をランプアップすることができます。
しかし、時間の経過とともにバーナー先端が燃料圧力で侵食されたり、TEG流とバーナー火炎の再循環によって火炎安定器がゆがんだり、バーナーエレメントがたるんだりすると(図2)、実際の燃焼や完全燃焼が起こる前に燃料がバーナー先端の下流にさらに流れるようになる。これらの要因により、火炎はチューブに衝突するまで長く成長する。時間の経過とともに、衝突は管を破壊する。この問題を改善しなければ、将来の故障が間近に迫っている。このケースでは、バーナーチップの腐食によって炎が長くなり、インピンジメントが発生した。
チャレンジ
このプロジェクトには、一般的な課題と状況特有の課題の両方が含まれていた。具体的には、事前に計画された運転休止は春に18日間予定され、非大規模運転休止に分類されていた。つまり、この運転休止中に燃焼タービンや蒸気タービンの改造を完了する予定はなかった。多くのサイトでは、運転休止はかなり前に計画されるのが普通であるため、ダクト・バーナー設備の現状を把握し、既存の計画運転休止スケジュールを中断したり変更したりすることなく、交換を完了できるようにすることが非常に重要である。
顧客はさらに、この設備はグリッドにとって重要であり、蒸気生産とメガワット出力の需要は、膨大な顧客基盤のために最も重要であると説明した。停電のタイミングを逃すという選択肢はなく、ユニットは停電の最終日に稼働していなければならなかった。このサイトの次の計画停電は数年先であったため、機器と設置にもうひとつ重要な考慮事項が加わった。このタイミングの課題に対応するためには、広範なターンキー計画が必要であり、施設との絶え間ないコミュニケーションが重要でした。
一般的に、設計と設置は、事前に承認された資本予算の停電時のコスト値内に収まらなければならない。このケースでは、新しいバーナーを購入するおよそ2年前に、顧客は資本予算を承認していた。しかし、経済内のインフレと再セントの大流行により、材料価格が予期せぬ懸念となった。
見積もり依頼のタイミングと、設置の停止日のタイミングが成功の鍵だった。設計、製作、配送、設置はそれぞれ、全体スケジュールのうち何週間かを消費する。そのため、計画された運転停止スケジュールのかなり前に機器を発注することが極めて重要だった。ここでも、ダクト・バーナー設備の現状を把握することで、施設オーナーは適切な交換計画を立てることができた。
プロジェクト・プロセス
この改修の設計は、ダクト・バーナーのターンキー交換プロジェクトを数多く成功させてきた経験豊富なチームが担当した。エンジニアとマネージャーからなる1つのチームをプロジェクトに参加させることで、顧客チームとの関係が強化され、プロジェクト全体の情報格差が解消された。
Zeeco 、国際標準化機構(ISO)プログラムによって監視された広範な承認メーカー・リストを利用している。このため、バイヤーには絶大な購買力があり、新しいサプライヤーやテストを受けていないサプライヤーに関する心配は無用である。
Zeecoの7つのグローバル製造施設のうちの1つでの機器の製造は、品質保証/品質管理(QA/QC)チームとプロジェクト実行エンジニアリングチームによって厳しく監視された。配送は、輸送の専門家からなるロジスティクス・チームによって計画・実行された。プロジェクト実行段階に先立ち、Zeeco 、現場で実施されるすべての機械・電気工事について、非常に具体的なターンキー・タスクごとの概要と計画を作成した。実施された計画には、経験豊富な建設作業員が従った。
ディスカバリー
ほぼすべてのターンキー設置プロジェクトでは、既存設備の解体を開始する前に、未知の問題を特定する発見がある。このプロジェクトの場合、HRSGの炭素鋼ケーシング壁の深刻な内部腐食が発見されました(図3)。このような発見は、古いHRSGやダクトバーナー機器ではますます一般的になってきており、特にHRSGユニットがもともと馬油環境の近くに設置されている場合や、極端な温度差によって露出したケーシング、密閉されたHRSG壁の断熱材、HRSG内部のフローティングライナープレートシステムが非常に過酷な働きをするような場所に設置されている場合に起こります。
これらのタイプのHRSGとダクトバーナーに関する他の一般的な発見は、燃料配管の内部腐食、圧力配管の肉厚減少、バルブシートの腐食や破壊である。これらの問題は、天候や季節の変化により、プラントの燃料配管インフラ全体で燃料温度が変動するため、時間の経過とともに発生します。このプロジェクトでは、外部配管を腐食のない新しい配管、継手、バルブに交換することがすでに予定されていた。
ソリューション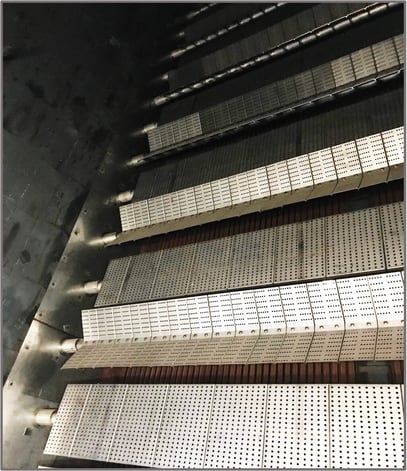
このターンキー・ダクト・バーナー交換プロジェクトは、そうした一般的な発見を念頭に置いて計画された。各発見の可能性は、機器の購入とターンキー設置の最終決定前に顧客と協議されます。詳細な計画によって前もって発見を軽減することで、実際のシナリオにできるだけ正確なパフォーマンス・スケジュールが作成され、サプライズの排除に役立ちます。
計画停電中は、他の請負業者が冷却塔やボイラドラムの腹パン、リリーフバルブなど、他の機器の作業を現場で行っていることが多い。現場は混雑し、工具トレーラーや工事事務所スペースが資材のステージングゾーンを狭めてしまうこともある。信頼できる設置会社を利用し、停電ミーティングへの毎日の出席を確保することで、すべての請負業者が毎日、懸念事項や先読み計画を発言し、共有することができる。請負業者間の調整により、クレーンや天井走行リフトのスペースや非破壊検査X線透視検査のクリアランスをめぐる競争や、資材や消耗品の搬入による道路の混雑といった問題を避けることができる。よくコミュニケーションされたプロジェクトは、より安全なプロジェクトであり、事故をなくし、人命を救う可能性がある。
成果とメリット
このプロジェクトの始動と設置作業員の復員後、この顧客にとってのメリットは非常に明確でした。以下の各ポイントが顧客のニーズを満たし、長年必要とされていたダクト・バーナー・システムに再び命を吹き込んだのである。
ターンキー・サクセス
ダクトバーナーの交換は18日間ではなく16日間で完了し、運転休止の最終日に無事再稼働することができた。
コスト
このケースでは、Zeeco'のグローバルな購買力により、チームは資材を調達し、機器購入のはるか前に作成された当初の資本予算額を節約することができた。
新しい設備
現在、顧客は以前の問題のない新しいダクト・バーナー・システムを手に入れた。メンテナンスと運転コストの削減による経済的な節約は、長期にわたる節約につながります。
正しい機材
設計と設置は仕様に100%準拠しており、顧客は1回の停電と予算内で、要求されたすべてを手に入れたことになる。
ヒートリリース
この新しい装置は、最適な蒸気生産のために、HRSGボイラーに適切な放熱量を供給する。
ファブリケーション
Zeeco 社内に7つあるグローバルな製造施設の1つを活用し、社内と顧客の両方のQA/QC要件に完全に準拠した装置を納期内に完成させた。
配送
サプライヤーのロジスティクス・システムを利用して、購入した機器が現場に配送されることが分かっていたため、顧客管理の監視と懸念に費やす多くの時間を節約することができた。
インストール
このターンキー設置は、Zeeco が使用・管理している多くの機械・電気設置チームのひとつを利用した。完全なターンキー設置により、顧客は管理監督と懸念に費やす多くの時間を節約することができた。
オンタイム・パフォーマンス
プロジェクトは予想より早く、予算内で完了し、生産者に利益をもたらし、計画された停電が正しく、延長の必要がないことを確認した。
安全事故ゼロ
全員が毎日、怪我をすることなく帰宅した。長期的には、保険料は低いままであり、施設の安全追跡指標は無傷のままであり、会社の安全記録は傷ひとつないままである。
アクセス向上
バーナー前面のアクセスエリアが混雑していないため、メンテナンスや運転がしやすく、安全な作業環境を実現します。
トレーニング
完璧なオペレーションを達成し、不必要な出張を減らすためには、サプライヤーから新しい機器についてオペレーション・チームのトレーニングを受けることが不可欠である。
排出量
新しい設備技術を導入することで、多くの場合、排出量が大幅に削減され、事業会社は排出量の許容範囲内にとどまることができるようになる。
機器保護
HRSG炉内にうまく固定された火炎形状と、HRSG炉内にうまく収まる長さの火炎により、下流の管セクション、ライナー壁、天井、床へのダメージが排除される。
全米防火協会(NFPA)への準拠
ダクトバーナーの管理団体であるNFPA85、特に第8章は、一般的に更新されている。設備が新しいということは、安全対策がすでに施されているということである。
保証
新しい設備は、施設所有者に限定的な保証を提供する。